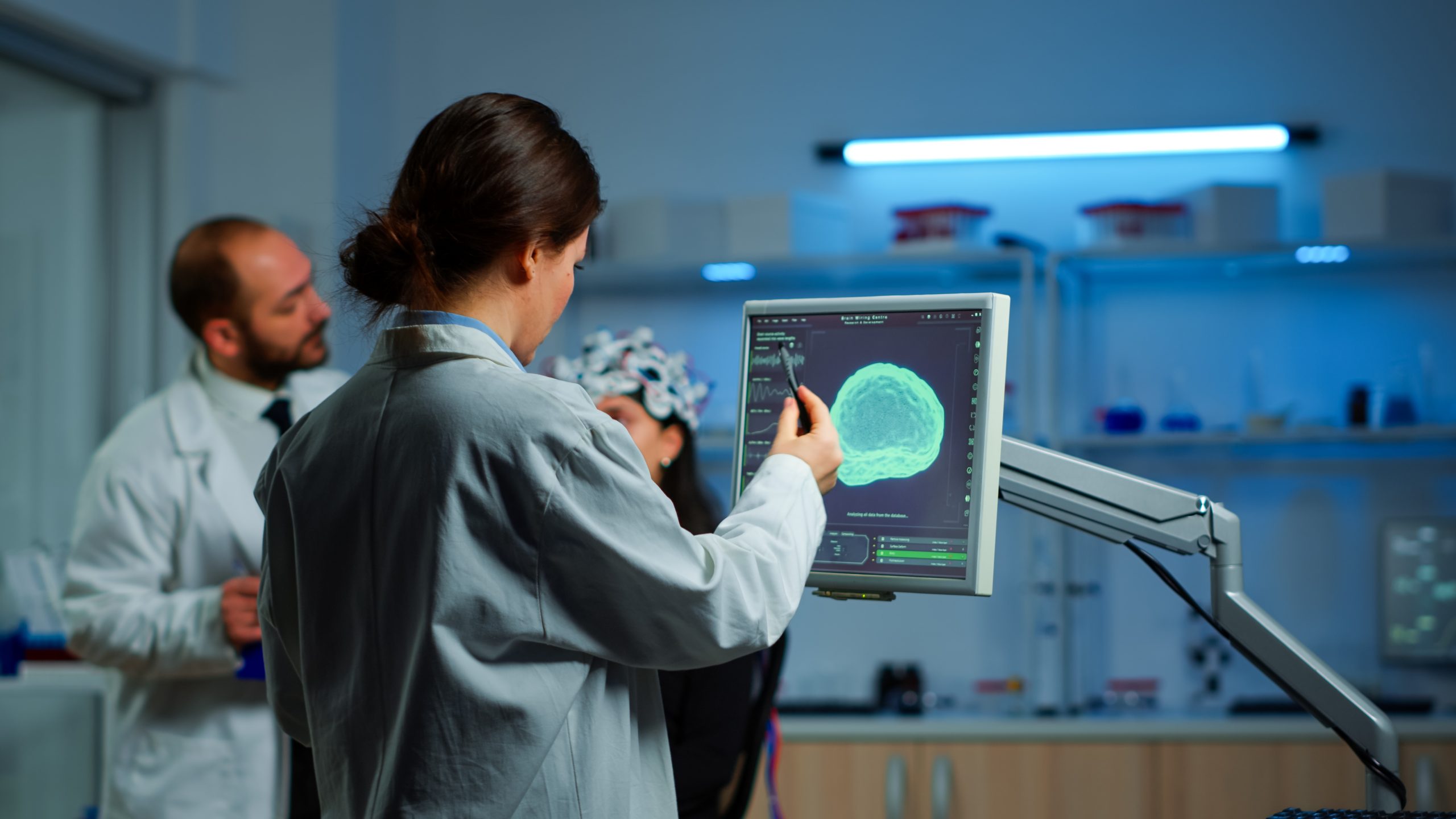
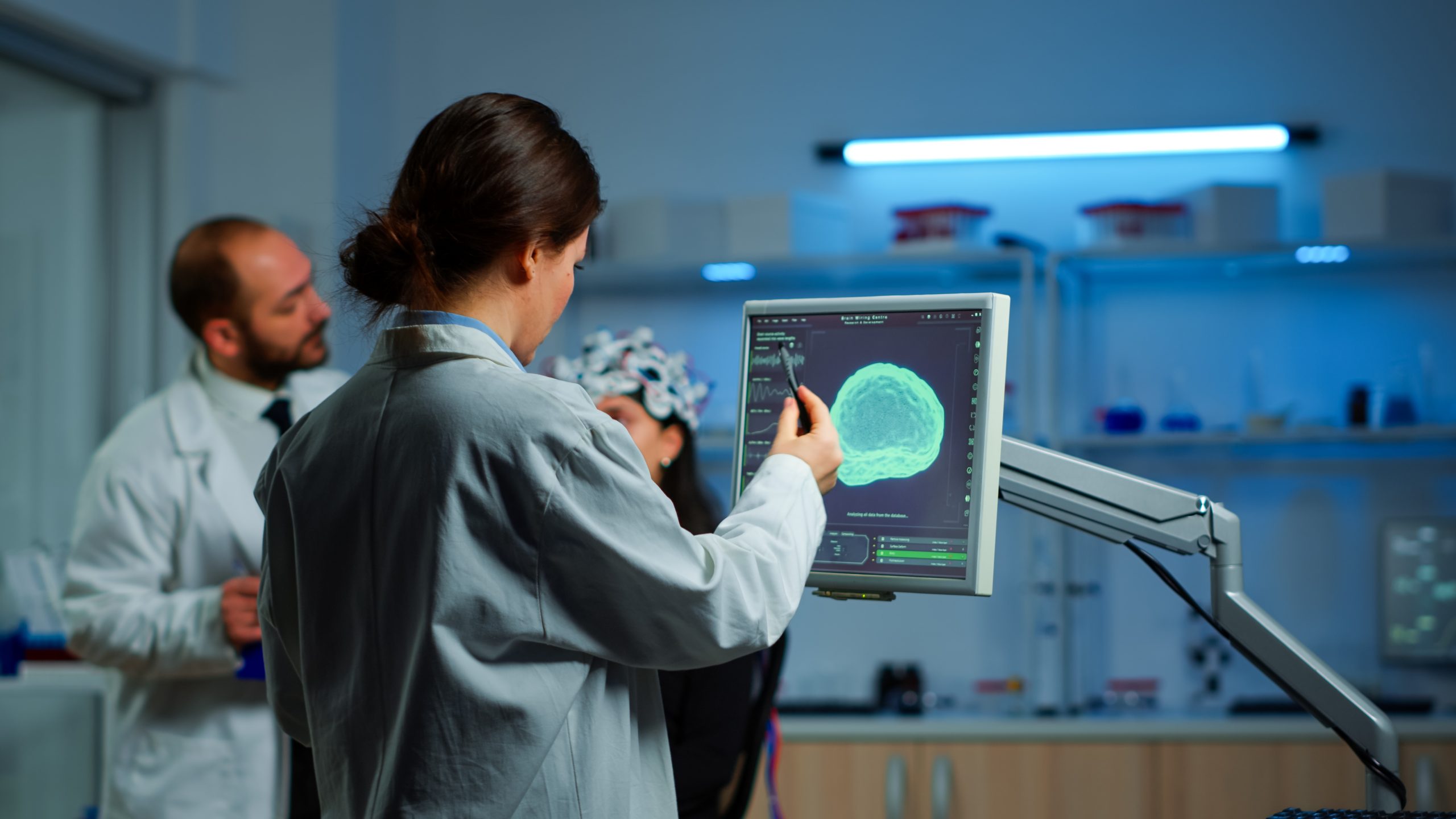
According to our research, which was just published in Science, a new 3D printing method utilizing silicone can create precise models of the blood arteries in your brain, allowing neurosurgeons to conduct neurosurgery with more exact simulations before they operate.
Before entering the operating room, many neurosurgeons simulate each neurosurgery using models of the patient’s brain. However, the training models that neurosurgeons currently employ don’t accurately simulate actual blood arteries. They give unreliable tactile feedback, are deficient in small but crucial structural details, and frequently omit entire anatomical elements that affect how each procedure during neurosurgery will be carried out. Pre-operative simulations using personalized and realistic patient brain reproductions may help to minimize mistakes during neurosurgery.
However, copies made with 3D printing could have the supple texture and precise structural design that surgeons require.
Typically, 3D printing is pictured as a process that involves building up a self-supporting structure layer by layer of melted plastic. Unfortunately, unlike the plastic filament that most 3D printers use, many soft materials do not melt and then resolidify. With soft materials like silicone, users only get one chance because they must be printed while they are still liquid and then irreversibly solidified.
How can a complex 3D shape be created out of a liquid without it turning into a puddle or a blob that is slumping?
For this, researchers created a broad strategy known as embedded 3D printing. This method involves depositing the “ink” into a bath of a second supportive substance that is intended to flow around the printing nozzle and trap the ink in the area immediately after the nozzle retracts. By holding liquids captive in three dimensions until it is time to solidify the printed structure, enables users to build complicated structures out of liquids. Structures made of a range of soft materials, including hydrogels, microparticles, and even living cells, have been successfully created via embedded 3D printing.
However, silicone printing has proven difficult. While the majority of support materials are water-based, liquid silicone is an oil. The reason why oil droplets in water adopt a circular shape is due to the high interfacial tension between oil and water. Even in a support medium, this force can cause silicone structures that were 3D printed to deform.
Even worse, while being printed, these interfacial forces cause small-diameter silicone features to shatter into droplets. Silicone materials that can be printed without a support have undergone extensive modification, but these changes also affect the silicone’s softness and stretchability, which are important to users.
We chose to address the issue of interfacial tension by creating a support material made of silicone oil because we are researchers working at the intersection of soft matter physics, mechanical engineering, and materials science.
In order to significantly reduce interfacial tension, we hypothesized that the majority of silicone inks would be chemically related to our silicone support material while simultaneously being sufficiently dissimilar to maintain their separation when assembled for 3D printing. We generated various potential support materials but found that the optimum strategy was to make a dense emulsion of silicone oil and water. It can be compared to a clear mayonnaise comprised of tightly packed microdroplets of water suspended in a continuous silicone oil stream. This process is known as AMULIT, or additive manufacturing at extremely low interfacial tension.
We were able to print commercial silicone at high resolution and produce features as small as 8 micrometres (or about 0.0003 inches) in diameter using our AMULIT support medium. The fabricated structures are equally strong and stretchable as their conventionally moulded equivalents.
Our ability to 3D-print accurate models of a patient’s cerebral blood arteries from a 3D scan as well as a working heart valve model based on typical human anatomy was made possible by these capabilities.
From common consumer goods like cookware and toys to cutting-edge technologies in the electronics, aerospace, and health care industries, silicone is an essential component of countless products.
Typically, silicone items are created by injecting or pouring liquid silicone into a mold, allowing the cast to harden, and then extracting the finished object. Manufacturers can only produce things in a limited number of specified sizes, shapes, and designs due to the cost and difficulty of producing high-precision moulds. Another challenge is removing fragile silicone structures from moulds without causing harm, and manufacturing flaws rise when moulding extremely complex structures.
By overcoming these obstacles, the medical field may be able to develop breakthrough silicone-based technologies that could revolutionize care through the use of customized implants or patient-specific replicas of physiological components.
more recommended stories
Hemoglobin as Brain Antioxidant in Neurodegenerative Disease
Uncovering the Brain’s Own Defense Against.
Global Data Resource for Progressive MS Research (Multiple Sclerosis)
The International Progressive MS Alliance has.
AI Diabetes Risk Detection: Early T2D Prediction
A new frontier in early diabetes.
Cancer Cells Learn to Self-Report: A New Frontier in Immunotherapy
How a Drug Complex Enables Immune.
Staphylococcus Shows Complex Enzyme Redundancy, Study Finds
A Bacterial Pathogen That Refuses to.
Parkinson’s Disease Care Advances with Weekly Injectable
A new weekly injectable formulation of.
New Blood Cancer Model Unveils Drug Resistance
New Lab Model Reveals Gene Mutation.
Osteoarthritis Genetics Study Uncovers New Treatment Hope
Osteoarthritis- the world’s leading cause of.
Antibody Breakthrough in Whooping Cough Vaccine
Whooping cough vaccine development is entering.
Scientists Unveil Next-Gen Eye-Tracking with Unmatched Precision
Eye-tracking technology has long been a.
Leave a Comment